Sustainability
During production of stainless steel, unwanted metal oxides are being formed on the surface of the material. This site gives an overview of the chemical reactions taking place through pickling – a process to remove the formed oxides.
.jpg)
Filter Sludge
Traditional Steel Pickling processes.
The acids, which are used for pickling, are only consumed to a certain degree. The formed metal salts lower the reaction rate and start to precipitate in the pickling bath. As a consequence, the acid solutions have to be disposed at a time when still a large portion has not reacted yet. These waste solutions contain free unreacted acids, spent acids and dissolved metal components, forming the so called “waste acid”.
Need for Waste Acid Disposal
Before the waste acid can be discharged into the environment, it is typically diluted with water and neutralized with Ca(OH)2 forming calcium fluorides and calcium nitrates as well as metal hydroxides. The fluorides and the hydroxides precipitate and can be separated through a filtration process. As a result, toxic sludge and nitrate-containing wastewater is generated. The sludge needs to be transported to a landfill for hazardous waste. Depending on the environmental limits, the nitrate-containing wastewater needs to be processed further in a wastewater treatment plant or can be directly disposed into the environment.
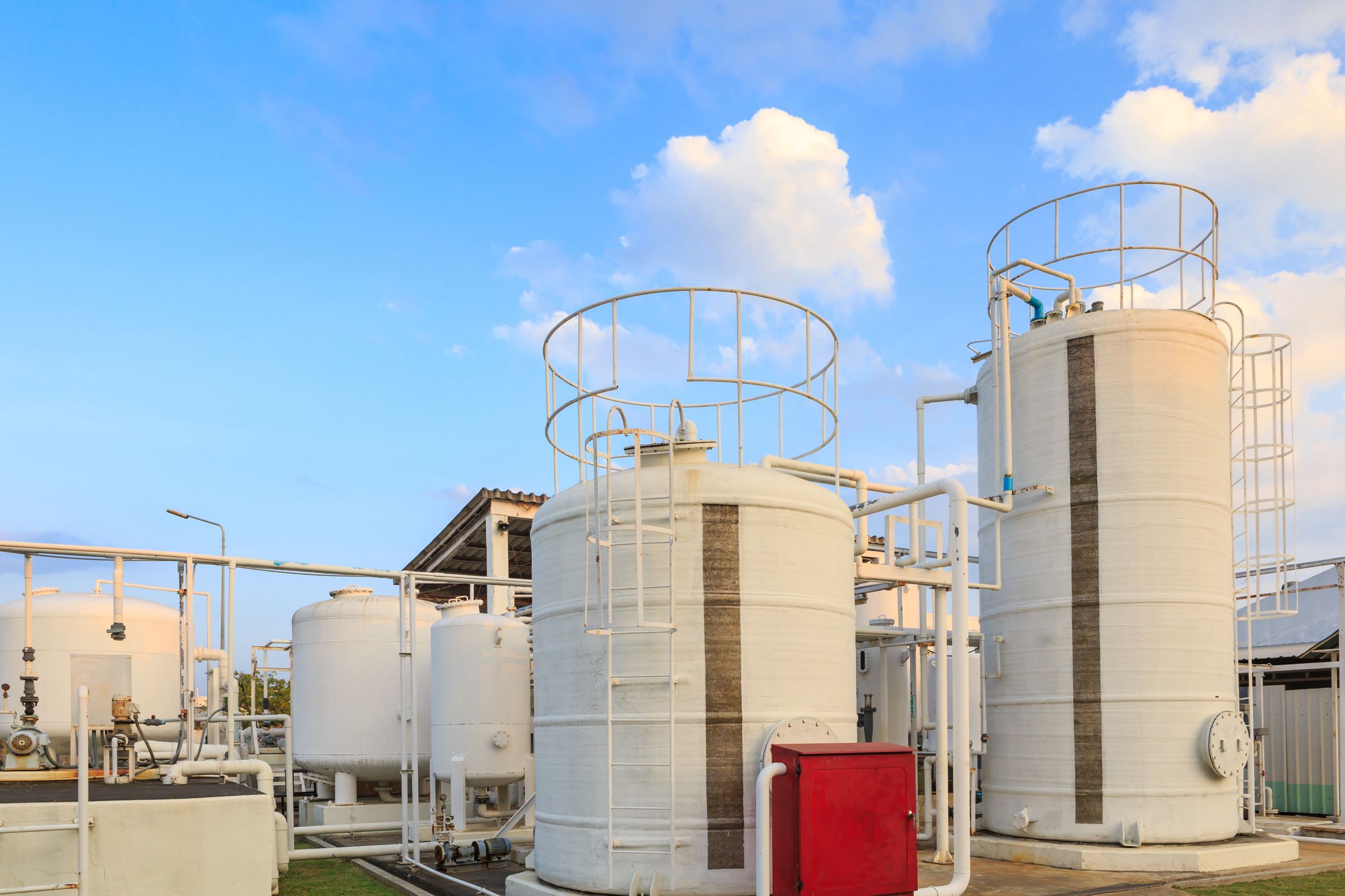
Acid Neutralization Plant
The Retarda purification process.
Purification processes like Retarda systems often use ion resins beds to partially remove the metal salts from the pickling bath. A branch stream is taken from the pickling bath and the resin is loaded with metal salts from the waste acid. A fraction with less metals is sent back to the pickling bath, while the metal salts have to be cleaned off from the resin with water. This wastewater stream has to be treated in the neutralization process like in traditional steel pickling processes. The solution, which is sent back to the pickling baths, is enriched with fresh acids again in order to reach the desired concentrations for pickling.
Need for Waste Acid Disposal
A purification system will not eliminate the purchase of fresh acid; it will only reduce the quantity that is consumed. Neutralization of waste streams – with the need of waste water disposal and sludge landfilling – is still necessary as well as complete exchange of the bath from time to time.
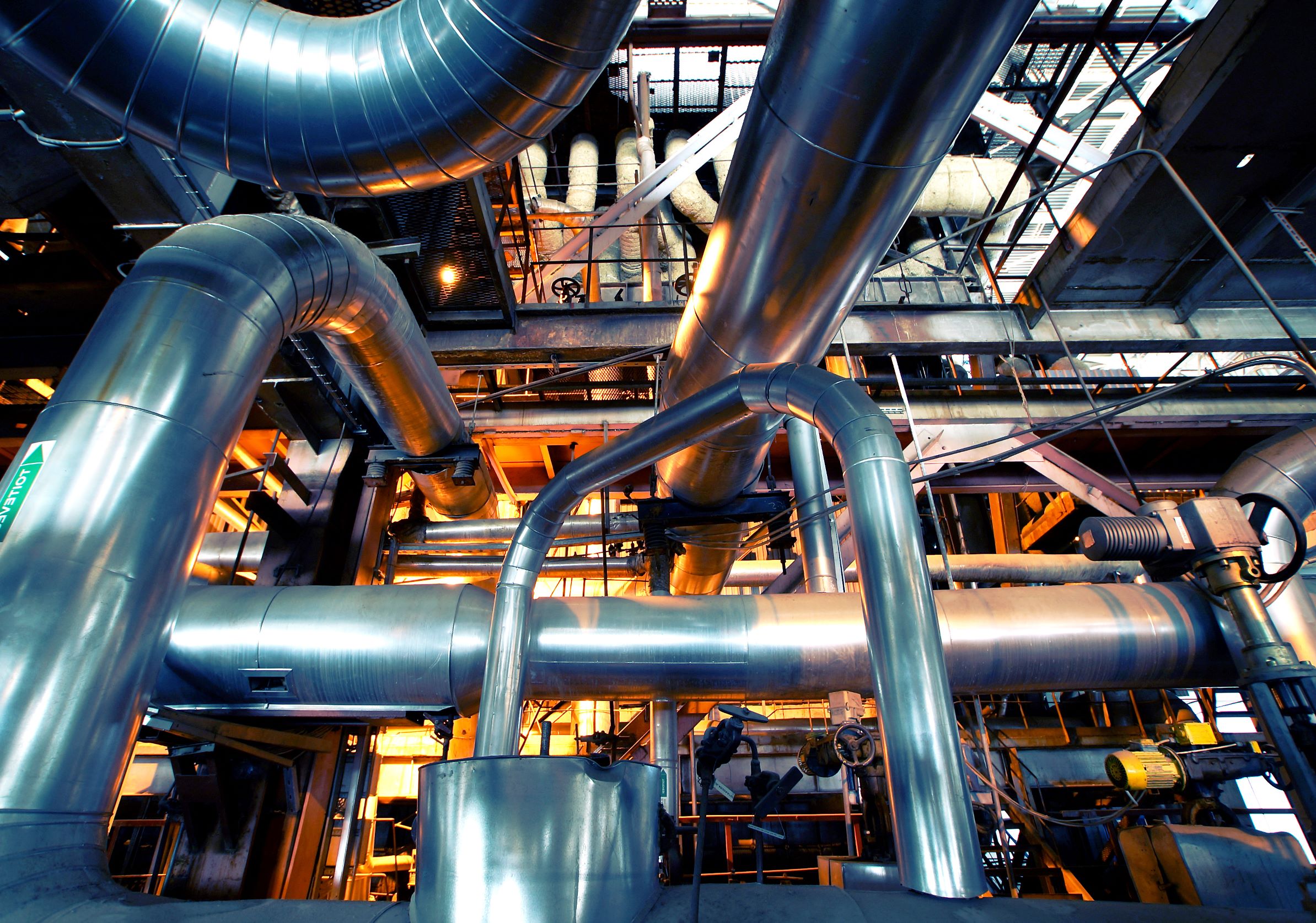
Acid Regeneration Plant
Regeneration Processes
A regeneration process in stainless steel pickling aims to convert metal salts back into usable acids, such as hydrofluoric (HF) and nitric (HNO₃) acid, and recover these acids in their free form. By breaking down waste acids, this process produces two valuable products: metal oxides and regenerated acid. These products can be reintroduced into the steelmaking and pickling process, creating a closed-loop system that maximizes resource efficiency. The technologies available today are Spray Roasting Technology or REGMAX® Technology.
Spray Roasting for Waste Acid
Spray roasting is currently the most widely used regeneration process for hydrochloric waste acids from carbon steel pickling, and is also being adapted for the recovery of nitric and hydrofluoric acids; the process is best adapted to the needs of mixed acid recovery, but remains a compromise as it was not originally designed to meet the complex requirements of mixed acid recovery. The basic spray roasting process includes:
1. Evaporation: The waste acid is atomised into the spray roasting reactor where it is exposed to temperatures high enough to evaporate the acid.
2. Pyrohydrolysis reaction: At the same time, the high temperature facilitates a pyrohydrolysis reaction in which the metal salts in the waste acid are converted to metal oxides.
3. Formation of acid gas and metal oxides: The acid in the waste stream is partially converted into acid gas, while the metal salts are converted into fine metal oxide particles. One of the major drawbacks of spray roasting technology is that the nitric acid fraction decomposes to NOx gas, resulting in a loss of nitric acid and a NOx waste gas problem. The regenerated hydrofluoric acid can be recovered in an absorption process and the metal oxides are collected as a by-product
NOx Formation during Spray Roasting
As can be seen above, one of the major limitations of spray roasting technology is the formation of nitrogen oxides (NOx). Nitric acid partially decomposes into NOx gases under high temperature conditions, which presents several challenges:
- Acid loss: A significant amount of nitric acid is lost in the form of nitrogen oxides rather than being recovered as HNO₃ gas. This reduces the efficiency of acid regeneration and increases the need for fresh acid input into the pickling process.
- Environmental concerns: To control NOx emissions, DeNOx systems (such as Selective Catalytic Reduction or SCR) are required to treat the exhaust gas before it is released. These systems reduce NOx emissions but add operational complexity and cost to the spray roasting process. SCR systems require a catalyst and additional reactants, such as ammonia, which increase resource consumption and generate secondary waste, further impacting cost efficiency and environmental performance.
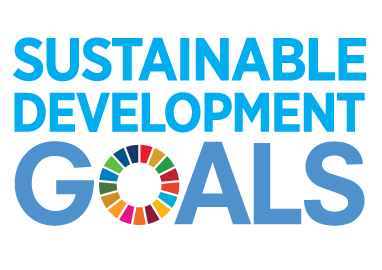
Our REGMAX® Technology
The most complete solution on the market is SUSTEC's REGMAX® technology to overcome all the problems associated with mixed acid pickling and its regeneration. No sludge or effluent is generated and no DeNOx unit is required as with conventional spray roasting technology. The recovery of the acid and metals can be considered almost complete. The intelligent utilisation of heat from waste streams from other processes additionally lowers the energy requirement of the recovery process.
Recovery rates of >99% for HF and >98% for HNO3 are achievable.
REGMAX not only reduces your production costs, it also meets 3 of the United Nations Sustainable Development Goals. A technology that is highly accepted by European authorities to meet the new guidelines for sustainable production COM/2020/98 final.